Our Research and Development projects
Flinders University
We are pleased to announce our ongoing research and development partnership with Flinders University, focusing on the application of Nano Technology in the production of composite springs for the automotive industry. This collaboration allows us to harness the potential of Nano Technology to enhance the performance and durability of automotive springs. By incorporating Nano Technology into the manufacturing process, we aim to create composite springs that offer superior strength-to-weight ratio, improved resistance to corrosion and fatigue, and enhanced overall performance. With the expertise and resources provided by Flinders University, we are confident in our ability to develop innovative solutions that will revolutionize the automotive industry. This partnership signifies our commitment to continuous improvement and our dedication to delivering high-quality products that meet the evolving needs of our customers.














TJ Wrangler Rear Coil Springs Test
Jeep Tj Wrangler testing the new Rear Coil Spring. This New Spring is made using Nano Technology

Predict the future by creating Understanding the static performance of composite helical springs with braided nested structures
Ling Chen, Joel Chong, Qian Jiang, Liwei Wu, Youhong Tangit
Application of composite helical springs (CHSs) is constrained by their poor static compression performance. In this study, a novel composite helical spring with a braided nested structure (BNCHS) is proposed. The fiber volume fraction (Vf) of BNCHS with braided angle of 15° and 30° (BNCHS15° and BNCHS30°) only increases by 0.9% and 1.8% respectively comparing with that of unidirectional composite helical spring with Vf of 55% (UCHS55%). The compression experimental results show that the spring constant of BNCHS15° and BNCHS30° can reach 105.4% and 171.4% higher than that of UCHS55% respectively. The internal mechanism of significantly improving compression performance of BNCHS is revealed by using a meso model. Numerical result shows that the mises stress of BNCHS15° and BNCHS30° can be 2.43 and 3.14 times higher than that of UCHS55% respectively. Finally, the resilience and specific spring stiffness of BNCHS and steel are compared, highlighting the obvious advantage of static performance of BNCHS.
Link:https://www.sciencedirect.com/science/article/pii/S1359835X23003986
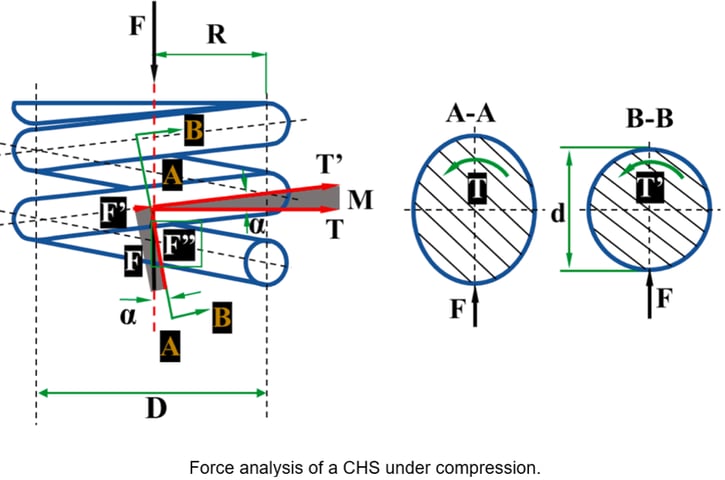
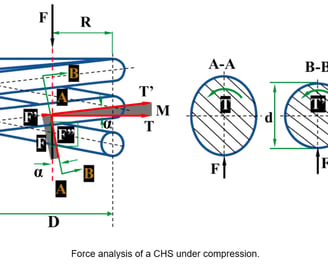
Understanding stiffness degradation of composite helical springs with multi-braided layers under impact
Ling Chen, Wenjin Xing, Joel Chong, Qian Jiang, Yiwei Ouyang, Liwei Wu, Youhong Tang
Understanding stiffness degradation and developing suitable damage detection method for composite helical springs (CHSs) are important for their application and further development. In this study, a coupled plasticity damage model for capturing stiffness degradation of CHSs with multi-braided layers (MBLs-CHS) is developed. Experimental results show that there is minor damage that only happens in the resin component of MBLs-CHS during impact. The element removal fraction in the simulation result is used to evaluate the damage severity, which is suggested to increase with impact energy (Ei) and decrease sequentially for CHSs with single, double, and triple braided layers (i.e., SCHS, DCHS, and TCHS). Specifically, damage severity of TCHS decreases by 51.3 % under 60 J impaction compared to that of SCHS. Finally, the time domain analysis method is introduced to monitor damage in real time. The amplitude intensity profiles under various Ei of CHSs have been fitted to predict the global stiffness degradation of CHSs in real time.
Link: https://researchnow.flinders.edu.au/files/132044845/Chen_Understanding_P2024.pdf
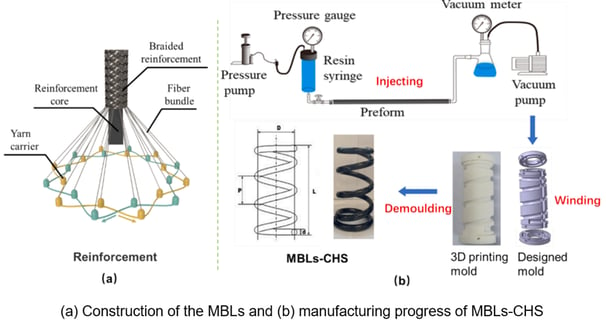
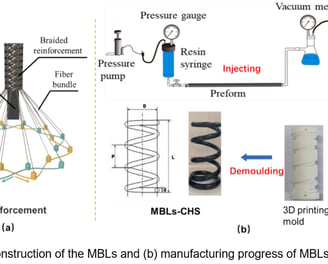
Analysing impact characteristics of composite helical springs with multi-braided layers based on virtual fiber model
Ling Chen, Wenjin Xing, Joel Chong, Qian Jiang, Yiwei Ouyang, Liwei Wu, Youhong Tang,
Heavy-duty springs can be made lightweight by replacing metallic materials with polymer composite materials. Most existing studies mainly concentrate on the static performance of composite helical springs (CHSs), un derstanding the dynamic impact of CHSs is limited. In this study, the impact response of CHSs with multi-braided layers (MBLs-CHS) is investigated using drop-weight impact tests. Experimental results indicate a sequential improvement in the impact performance of CHSs with single, double, and triple braided layers (SCHS, DCHS, and TCHS). Specifically, TCHS demonstrates enhancements of up to 5.1 %, 78.3 %, and 34.1 % in deformation resistance, Fmax, and Ee, respectively, compared to SCHS. Subsequently, a virtual fiber model (VFM) elucidates the internal mechanism behind this improvement. The force-bearing contribution of the corresponding braided layers in SCHS, DCHS, and TCHS is similar, emphasising that the impact response difference is primarily attributed to the additional braided layer. Additionally, stress and motion responses of VFM revealed non-linear characteristics in stress, displacement, and velocity waves transitioning of MBLs-CHS. Finally, the impact mitigation ability of MBLs-CHS can be calculated based on velocity responses of VFM, highlighting that of TCHS improves by 111.6 % and 42.0 % compared to SCHS and DCHS, respectively. This research establishes a robust foundation for dynamic studies and offers valuable guidelines for the engineering design of CHSs.
Link: https://www.sciencedirect.com/science/article/pii/S2452213925000087
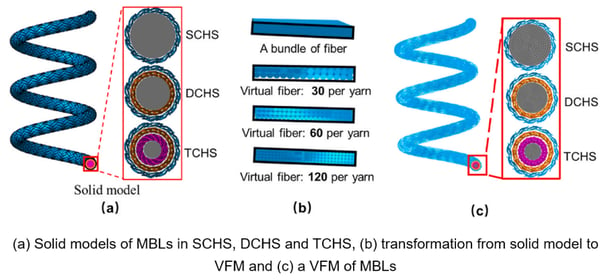
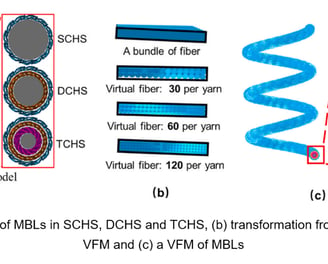
Understanding multiple parameters affecting static and dynamic performances of composite helical springs
Ling Chen, Wenjin Xing, Liwei Wu, Joel Chong, Tongda Lei, Qian Jiang, Youhong Tang,
Composite helical springs (CHSs) are mainly used in transportation and aerospace fields, such as automobile suspension, railway bogie and aircraft engine systems. It has become a trend to replace the traditional metal helical springs with CHSs with the advantage of energy conservation during service and emission reduction during manufacturing. The advantages of CHSs such as low weight, high specific strength, high specific modulus, corrosion resistance, fatigue resistance and high strain energy storage capacity mean that it has great development potential. The static and dynamic performances of CHSs together determine whether they can be used on a large scale in the engineering field. The static performance of the CHS determines their service-load range and the dynamic performance determines the service life and safety performance of CHSs under dynamic load environmental conditions. Therefore, it is an important task to optimize the static and dynamic performance of CHSs. To provide a reliable reference for the development of CHSs, this review analyzes the important factors affecting the static and dynamic performance optimization of CHSs from the perspectives of theory, finite element method (FEM), and experiment. In addition, the outlook in the research of CHSs are discussed.
Link:https://www.sciencedirect.com/science/article/pii/S2238785422011590
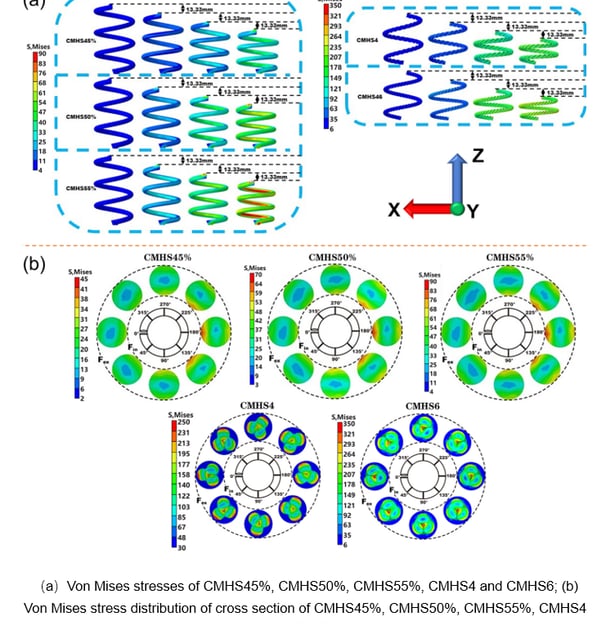
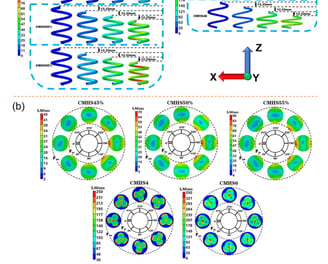
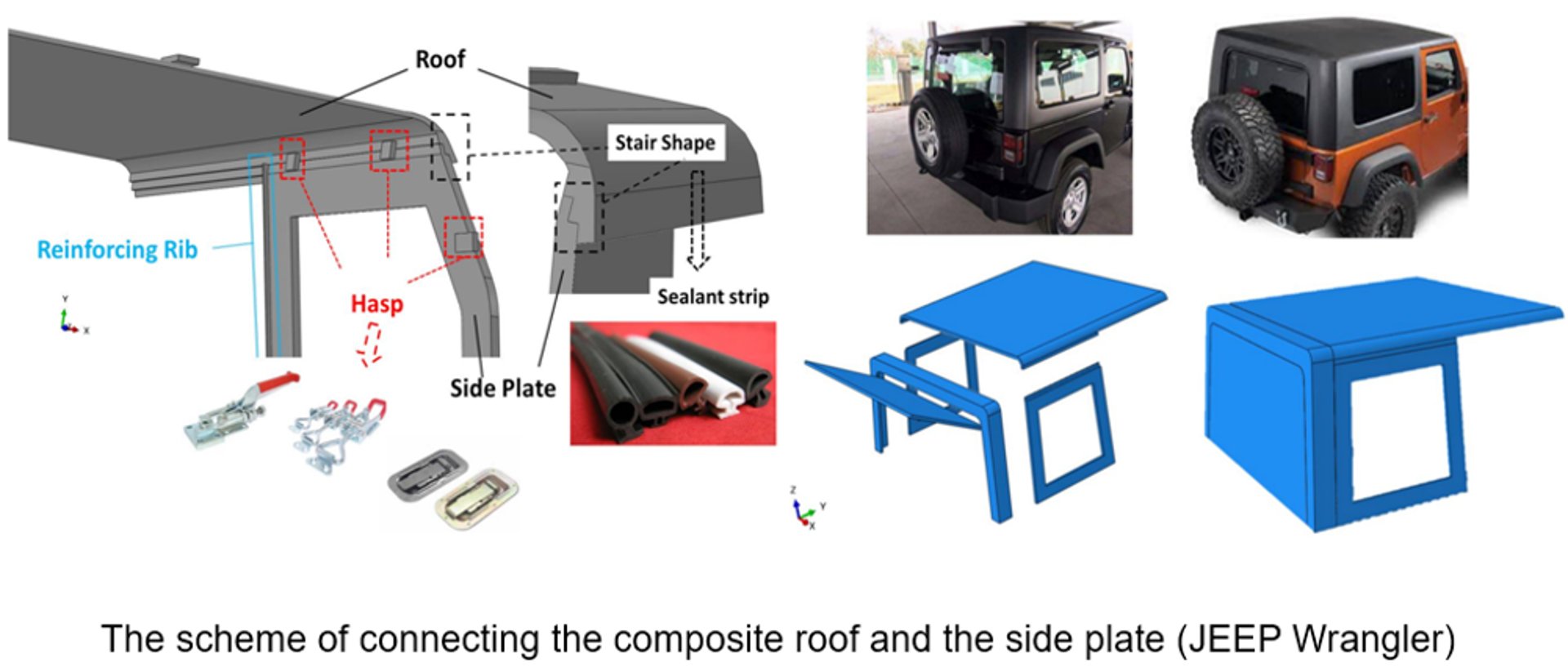